မော်တော်ယာဉ်ထုတ်လွှတ်မှုနှင့် လောင်စာဆီသုံးစွဲမှုဆိုင်ရာ ပိုမိုတင်းကျပ်သော စံနှုန်းများကို အကောင်အထည်ဖော်ရန် လိုအပ်ချက်များကြောင့် မော်တော်ယာဥ်လုပ်ငန်းတစ်ခုလုံးသည် အဆိုပါတိုးတက်မှုများကို ပြည့်မီရန် ရုန်းရင်းဆန်ခတ်ဖြစ်စေခဲ့သည်။လောင်စာဆီသုံးစွဲမှုနှင့် အိတ်ဇောထုတ်လွှတ်မှုကို လျှော့ချရန်အတွက် သမားရိုးကျနည်းလမ်းမှာ မော်တော်ကား၏အလေးချိန်ကို လျှော့ချရန်ဖြစ်သည်။ထို့ကြောင့် သွန်းသံအစား အလူမီနီယံအလွိုင်းဆလင်ဒါဘလောက်သည် ဖွံ့ဖြိုးတိုးတက်မှုလမ်းကြောင်းတစ်ခုအဖြစ် ပြောင်းလဲလာသည်။ထို့အပြင် အင်ဂျင်အတွင်း ပွတ်တိုက်မှုကို လျှော့ချခြင်းဖြင့် အင်ဂျင်၏ လောင်ကျွမ်းမှု စွမ်းဆောင်ရည်ကို သိသိသာသာ မြှင့်တင်နိုင်ပါသည်။ထို့ကြောင့် “cylinder Liner less” ၏ ကားအင်ဂျင်နည်းပညာအသစ်သည် ကားထုတ်လုပ်သူအများအပြား၏ အာရုံစိုက်မှုကို ဆွဲဆောင်ခဲ့သည်။
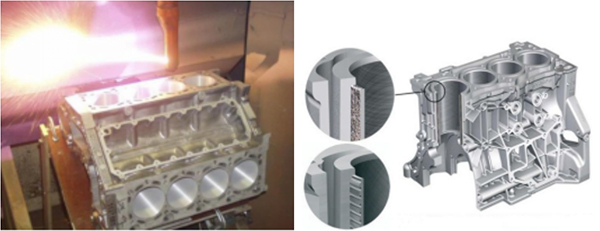
မော်တော်ယာဥ်အင်ဂျင်(များ) ဆလင်ဒါလိုင်ဒါနည်းနည်းပညာကို အပူဖြန်းခြင်းနည်းပညာကို မိတ်ဆက်ခြင်းဖြင့် ပြီးမြောက်အောင်မြင်ခဲ့ပါသည်။အင်ဂျင်ဘလောက်များ ထုတ်လုပ်မှု လုပ်ငန်းစဉ်အတွင်း အပူဖြန်းခြင်း အသုံးချခြင်းကို လုပ်ဆောင်သည်။ရေမှုန်ရေမွှားကို ကြိုတင်ပြုပြင်ထားသော အလူမီနီယံအင်ဂျင်ဆလင်ဒါပေါက်များ ၏ မျက်နှာပြင်ပေါ်တွင် သက်ရောက်သည်။ရေမှုန်ရေမွှားသည် သမားရိုးကျ သံဆလင်ဒါကို အစားထိုးရန်အတွက် ကာဗွန်နည်းသော အလွိုင်းအလွှာကို ဝတ်ဆင်ရန် ခံနိုင်ရည်ရှိသော အလွှာကို ပေါင်းထည့်သည်။liners မပါသော ဆလင်ဒါဘလောက်များကို လုပ်ဆောင်ရာတွင် အောက်ပါ အလုံးစုံစနစ်အစိတ်အပိုင်းများနှင့် အသုံးချပရိုဂရမ်များ ပါဝင်သည်-
● သွန်း
● ဆလင်ဒါဘလောက်ကို ကြမ်းတမ်းစွာ ပြုပြင်ခြင်း။
● ဆလင်ဒါဖေါက်ကို အထူအပါးဖြစ်စေသည်။
● မျက်နှာပြင်ကို အပူပေးလိုက်ပါ။
● အပူဖြန်းခြင်း။
● ပြီးအောင် ပြုပြင်ခြင်း။
● ဓားသွေးပြီးအောင်
ဆလင်ဒါနည်းသော လိုင်းနည်းပညာ၏ အဓိက လုပ်ငန်းစဉ်များကို coaxial မျက်နှာပြင်များပေါ်တွင် လုပ်ဆောင်သည် (ဆလင်ဒါမျက်နှာပြင်များ ပေးထားသည့် လေယာဉ်အတွင်း ဗဟိုပြုသောစက်ဝိုင်းများ ဖြတ်သွားသော မျဉ်းကြောင်းများပါရှိသော ဆလင်ဒါနှစ်ခုသည် ဤလေယာဉ်နှင့် ထောင့်မှန်ကျသော) ကြမ်းတမ်းသော ဆလင်ဒါမျက်နှာပြင်ပေါ်တွင် လုပ်ဆောင်သည်။ဤသည်ကို သဘောပေါက်သည်-
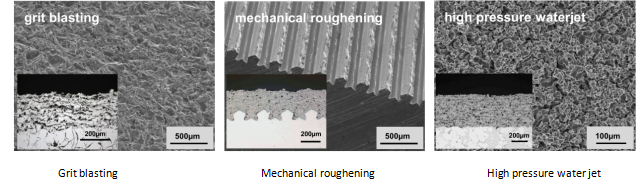
မျက်နှာပြင် ကြမ်းတမ်းခြင်း၏ ရည်ရွယ်ချက်မှာ အပေါ်ယံလွှာကို အလွှာ၏ မျက်နှာပြင်နှင့် စက်ပိုင်းဆိုင်ရာ ချိတ်ဆက်နိုင်စေရန်၊ အပေါ်ယံလွှာ၏ စက်ပိုင်းဆိုင်ရာ အကိုက်အခဲခံနိုင်မှုကို တိုးမြင့်စေပြီး မျက်နှာပြင်ကို ပိုမိုအသက်ဝင်စေကာ ပိုမိုအားကောင်းလာစေသော မျက်နှာပြင်ဖွဲ့စည်းပုံတစ်ခုအဖြစ် တိုးလာစေရန် လိုအပ်ပါသည်။ စည်းနှောင်မှုအားကောင်းခြင်း။မျက်နှာပြင် ကြမ်းတမ်းခြင်းကို ကြမ်းတမ်းစွာ ဖောက်ထုတ်ခြင်း၊ စက်ပိုင်းဆိုင်ရာ ကြမ်းတမ်းခြင်းနှင့် ဖိအားမြင့် ရေဂျက်ကြမ်းခြင်းစသည့် နည်းလမ်းအမျိုးမျိုးဖြင့် လုပ်ဆောင်သည်။Grit blasting သည် အသုံးအများဆုံး ကြမ်းတမ်းသော ကုသမှုဖြစ်ပြီး သတ္တုမျက်နှာပြင် ကြမ်းတမ်းခြင်းအားလုံးကို အသုံးချပါသည်။
သတ္တုမျက်နှာပြင်များကို နောက်ပိုင်းတွင် သန့်စင်နိုင်ပြီး၊ ကြမ်းတမ်းပြီး သဲကို ဖောက်ထုတ်ပြီးနောက် အလွန်တုံ့ပြန်မှု ဖြစ်လာနိုင်သည်။ထို့နောက် ကြမ်းတမ်းသော မျက်နှာပြင်ကို ပက်ဖြန်းခြင်းလုပ်ငန်းစဉ်ကို အသုံးမပြုမီ ဆီကင်းစင်သော ဖိအားမြင့်လေဖြင့် သန့်စင်သည်။
စက်အသုံးပြုခြင်းဖြင့် ကြမ်းတမ်းခြင်း (Surface Activation) ကိုလည်း လုပ်ဆောင်နိုင်ပါသည်။အလူမီနီယမ်မျက်နှာပြင်ကို အသွင်အပြင်တစ်ခုအဖြစ် ပုံသွင်းသည့် လုပ်ငန်းစဉ်များရှိပါသည်။၎င်းကို ဝင်ရိုးတစ်ခုတည်း စက်ယန္တရားစင်တာကို အသုံးပြုခြင်းနှင့် ထည့်သွင်းထားသော ဖြတ်တောက်ခြင်းကိရိယာများကို အသုံးပြုခြင်းဖြင့် လုပ်ဆောင်သည်။ဤသည်မှာ ကုန်ကျစရိတ်ထိရောက်သော ချဉ်းကပ်မှုဖြင့် ဝိသေသလက္ခဏာများကို ပြီးမြောက်စေရန် တစ်ကြိမ်တည်း လုပ်ဆောင်ခြင်းဖြစ်သည်။ရှေးကျသော အလွန်အနုစိတ်သော သွန်းသံဆလင်ဒါကိစ္စတွင်၊ အလွန်အကျွံ ကိရိယာ စုတ်ပြဲခြင်းသည် စီးပွားရေးအရ လက်ခံနိုင်စရာမရှိအောင် ဖန်တီးလေ့ရှိသည်။
ဖိအားမြင့် ရေဂျက်ကြမ်းဆွဲခြင်းသည် အလူမီနီယံဆလင်ဒါနှင့်သာ သက်ဆိုင်ပြီး သံပန်းဆလင်ဒါနှင့်လည်း မသက်ဆိုင်ပါ။Water jet လုပ်ငန်းစဉ်သည် ငွေကုန်ကြေးကျများသော ပွန်းပဲ့များကို အသုံးမပြုပါ။သို့သော်လည်း မျက်နှာပြင် ခြောက်သွေ့နေမှသာ အရည်ဂျက်ကို တိုက်ရိုက်အသုံးပြုခြင်း ပြီးမြောက်ပါသည်။ထို့ နောက် မျက်နှာပြင် ကြမ်းတမ်းမှုတန်ဖိုးသည် အခြားသော လုပ်ငန်းစဉ်များနှင့် နှိုင်းယှဉ်ပါက အတော်လေးနိမ့်ပါသည်။
ဆလင်ဒါမဟုတ်သောနည်းပညာတွင် အဓိကလုပ်ငန်းစဉ်တစ်ခုအနေဖြင့် မျက်နှာပြင်ကြမ်းတမ်းခြင်းသည် အပေါ်ယံပိုင်း၏ ချည်နှောင်ခြင်းခိုင်ခံ့မှုနှင့် အပေါ်ယံပိုင်းဆိုင်ရာ ဂုဏ်သတ္တိများကို တိုက်ရိုက်သက်ရောက်သည်။ထို့ကြောင့် ဆလင်ဒါနည်းဆလင်ဒါပိတ်ဆို့ခြင်းနည်းပညာကိုအသုံးပြုရာတွင် မျက်နှာပြင်ကြမ်းတမ်းခြင်းလုပ်ငန်းစဉ်ကို အာရုံစိုက်ရန် အရေးကြီးပါသည်။သင့်လျော်သော ကြမ်းတမ်းသောနည်းလမ်းကို ရွေးချယ်ခြင်းသည် မျက်နှာပြင်၏ အကောင်းဆုံးအသက်သွင်းမှုနှင့် ထုတ်လုပ်မှုထိရောက်မှုရရှိရန် အရေးကြီးပါသည်။
စာတိုက်အချိန်- မေလ ၂၆-၂၀၂၁